The goals were:
The result: up to 6A of fairly-quiet low voltage DC with 10-turn control of just a hair over 2V. Output voltage indication with 1mV resolution to 1.999V. Total success. It only *looks* like an unworkable bodge! :)
Click any image to see it full size and better quality
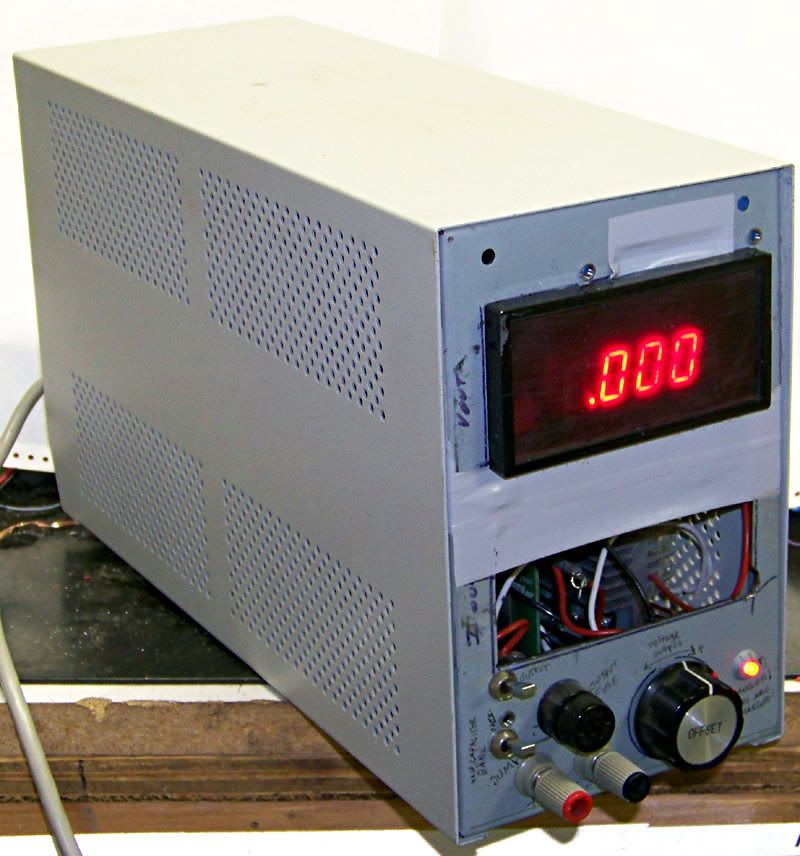
The mains power comes in to the supply filter from an old Compaq server power supply. I was having some difficulty getting the expected output from my prototype power supply; it was from this filter. There was a thermistor in the server to limit inrush current. The thermistor wastes a little power, and at low voltage I needed all of it. Jumpering across the thermistor gave me instant high current capacity.
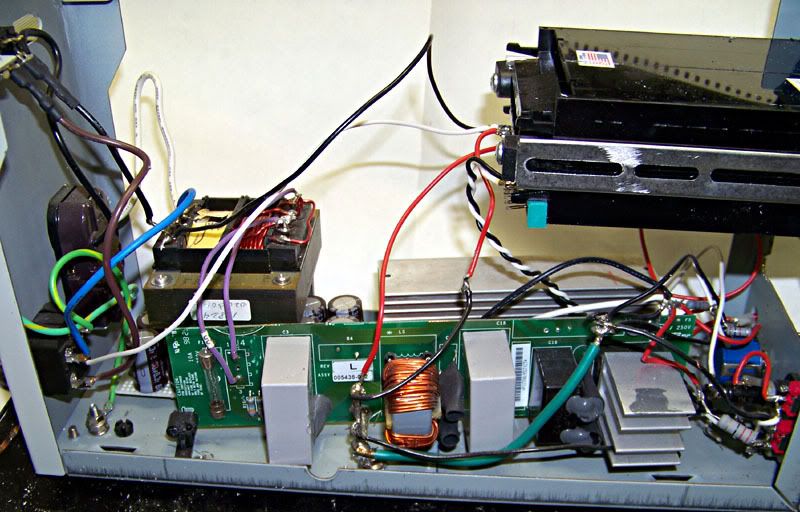
Then it's off to a transformer I snagged from a piece of medical equipment, unwound the secondary, and rewound it for the voltages I needed. It ended up with three secondaries with just a few dozen turns each of 16AWG magnet wire, which are wired in parallel. I put kapton tape between the layers of the winding and pulled each turn tight with the aid of a bench vise. It is pleasantly silent in operation.
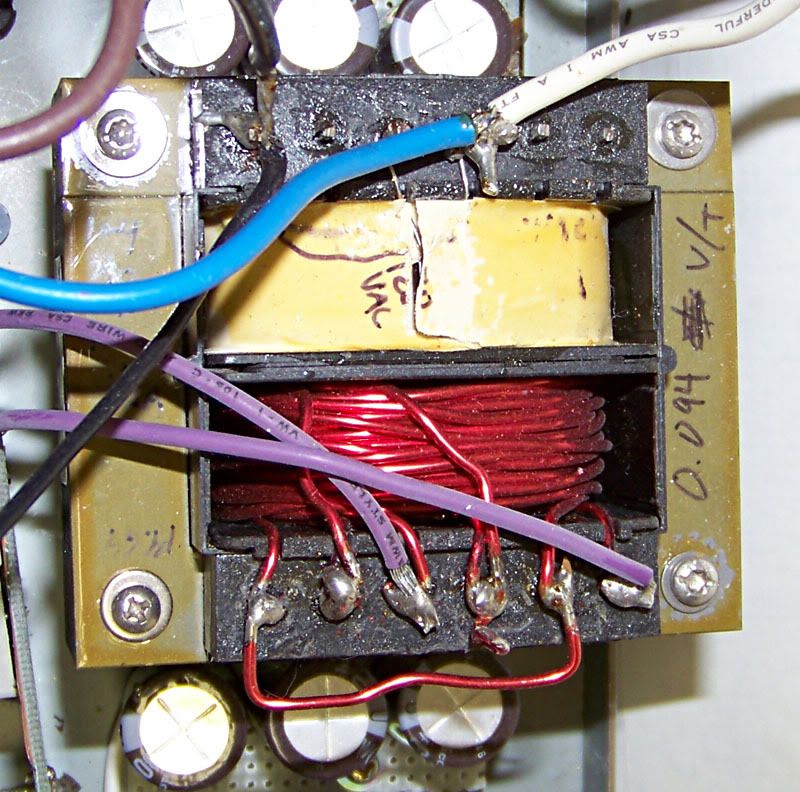
Then back to the filter PCB for rectification in a monolithic bridge rectifier with an excessively-large heat sink. From there it's off to a bank of capacitors (from a bunch of controllers for semiconductor wafer manufacturing chambers' vacuum level) in parallel for about 0.12F. This sits at almost exactly 5VDC when power is on. The actual circuit itself is pretty basic: A value-faked Bourns 10-turn pot sets the base voltage of a 2N6045 power transistor, which feeds eight 2n4918 power transistors their base current. These are mounted to a heat sink that also came from a computer power supply. The bus bars are more 16AWG magnet wire. The output transistors are wired in parallel and have 0.22 ohm resistors to help share the current load between them.
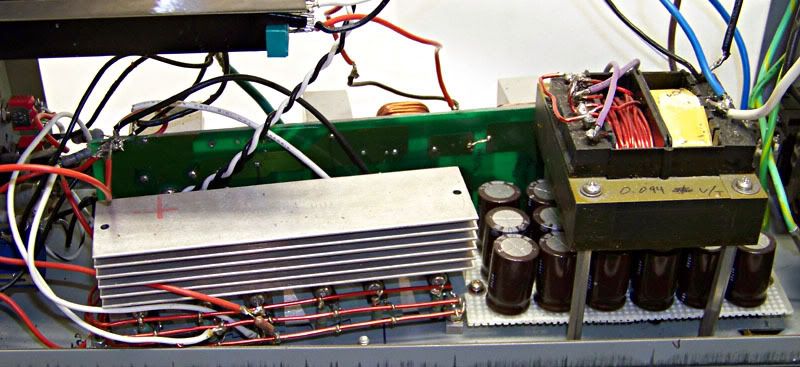
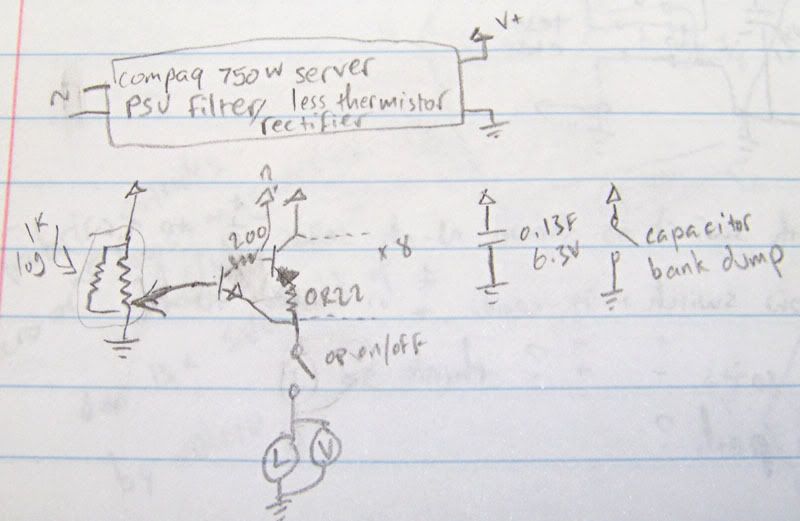
Yes, the schematic is somewhat lacking in detail. Those attempting this level of electronics tinkering will hopefully know what is meant. If you have no idea what is happening on this sheet of paper, take my word for it: it works.
The case used to be a Sola-brand UPS which had its guts recycled. It has a power outlet on the back, and I had power going in, so I figured "why not" and now there's an auxiliary mains power outlet on the back of my new power supply.
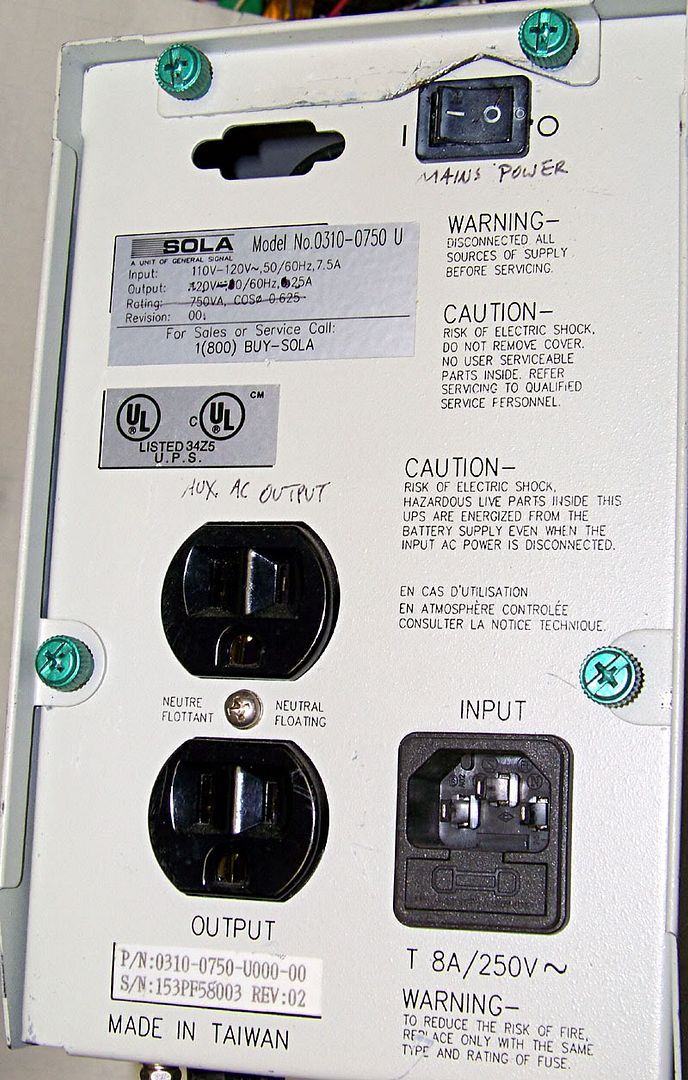
The knob is from an Olympus wafer inspection microscope station and binding posts come from a Hewlett-Packard analog RMS voltmeter.
The output voltage meter is a positively ancient 3.5 digit panel meter the brand of which I forget. At work we had to replace it because it was missing the red diffuser . . . at a cost of $250 to the customer. It is a type of meter made by everyone who does instrumentation. The case was damaged in addition to the missing diffuser, so I replaced it with a case from an Omega thermocouple readout acquired separately, years later. These things are amusingly ubiquitous and work great. This panel meter was calibrated against my bench meter from work and they agree perfectly; I called it good enough. There was going to be a second meter for current output monitoring, but it ended up being both more than zero effort AND the back of the meter would physically interfere with the filter PCB, so for now there's a hole in the front panel.
Don't stick your hand in there. The gray rectangle to the lower left of the big hole in the front panel is the bridge rectifier. A few inches deeper and you're dealing with 115V AC. Really don't stick your hand in there.
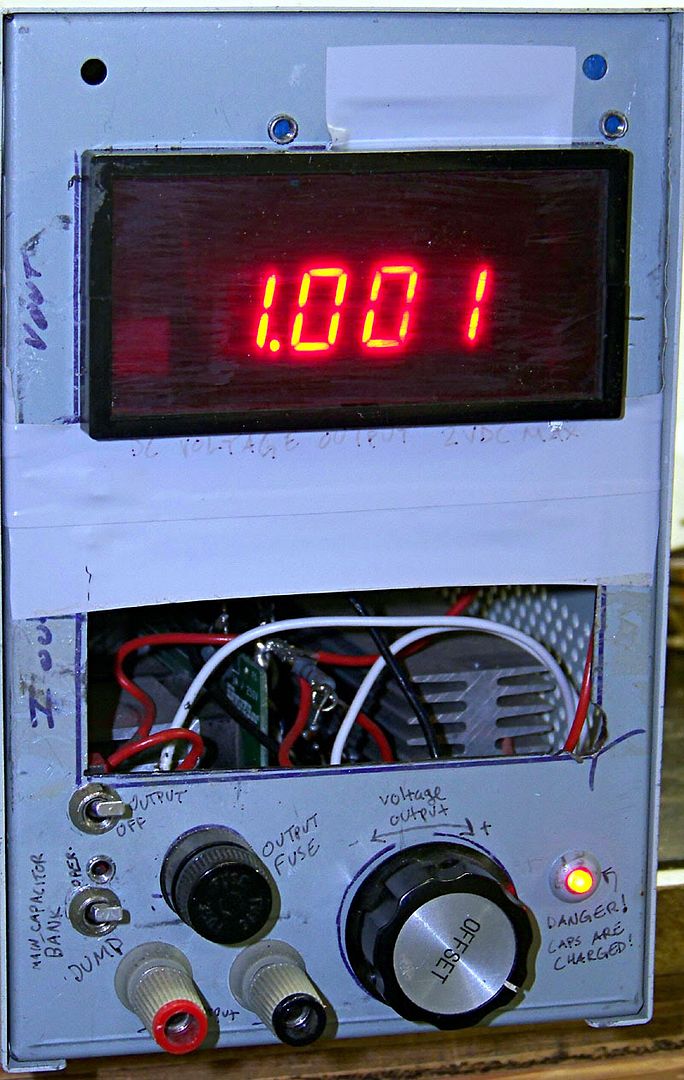
Safety: The mains input is switched and fused, the output is fused, and there is a switch to turn off the output. Because even at 5V, 0.12F is a lot of potential, I also installed a lamp to show that the capacitors are over half of their operating voltage, and a switch with a power resistor to bleed off the caps in under half a minute.
No comments:
Post a Comment